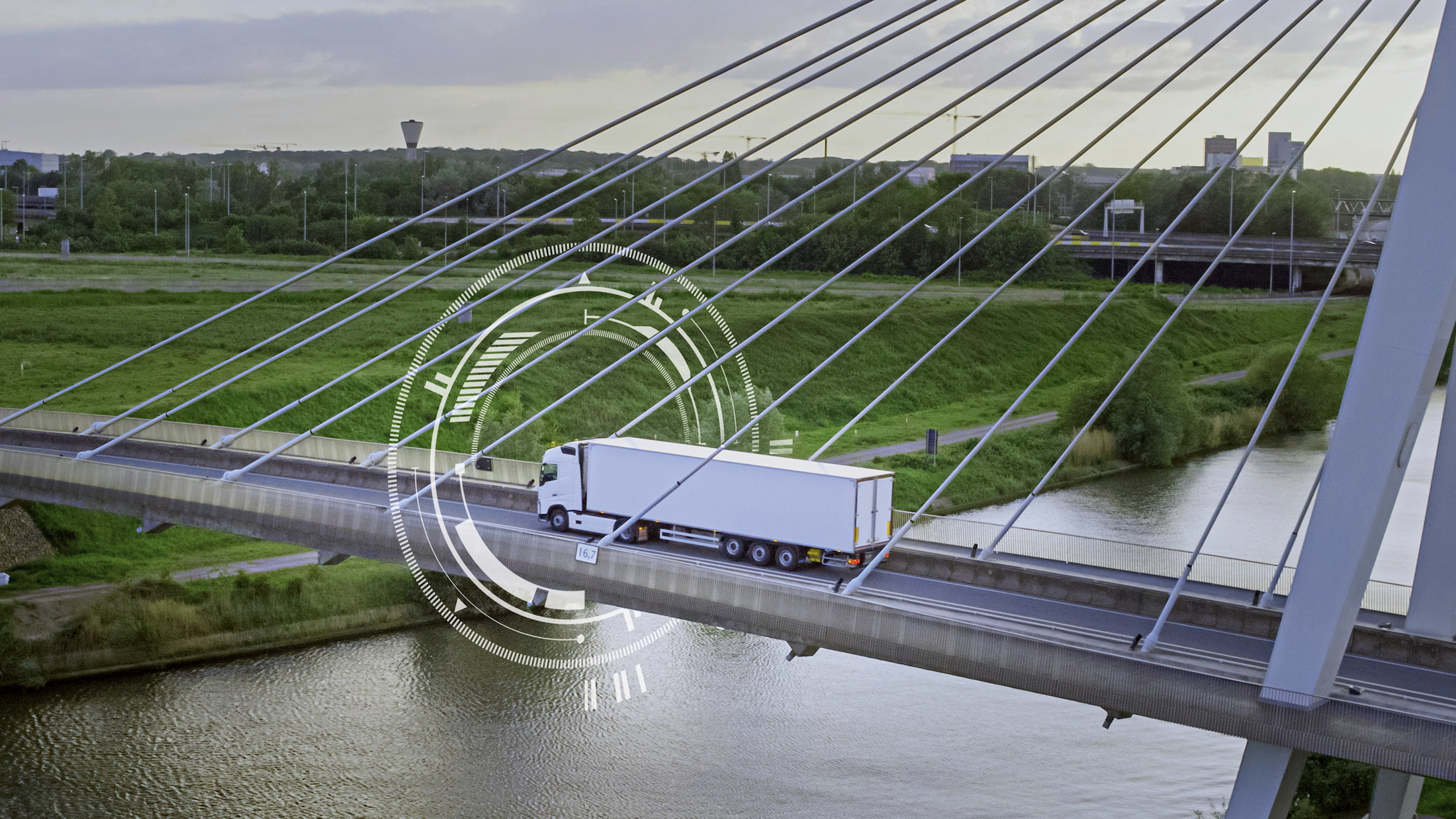
31st May 2023
<strong>Meet Mark: one of our experts delivering 24/7 fleet monitoring solutions</strong>
- Aftermarket
- Fleet Management
- Service
9 PM. The cooling unit in a rail container carrying special meats in the UK has stopped working. There are 5 hours left before the next trip, and once the train starts moving, there is no way to stop it. If allowed to leave, the meat on board will almost definitely spoil.
The situation looks bleak, but these types of challenges are exactly when Thermo King expert Mark shines. Since joining Thermo King in 1998, he has remained dedicated to getting Thermo King customers back out on the road as quickly as possible. “After serving 6 years in the Navy, I was drawn to the workshop bay where my passion as a technician was,” Mark reminisces. That passion for engineering and a knack for problem-solving means he reveled in the challenge of diving into the technical guts of Thermo King units and getting them moving again. And with his six like-minded colleagues, his workshop was eager to tackle any technical challenge that came their way.
The Uptime Center
In 2020, Thermo King created the Uptime Center for 24/7 Fleet Monitoring. Backed by years of experience and expertise and a belief in the power of connectivity, the Uptime Center aimed to enhance Thermo King’s services to its customers. After a successful pilot, ThermoKare 24/7 Fleet Monitoring officially launched in 2021. The Uptime Center now boasts a team of four additional experienced and certified Thermo King technicians, ensuring real-time delivery of uptime to customers.
The Uptime Center offers Mark all the engineering challenges he could ask for. Like the one rail container carrying special meats, stranded without cooling as daylight dwindles. High stakes, a time limit, and a complex problem. These are the kinds of challenges Mark lives for. Once he received the notification, he dove into TracKing data and found two possible culprits: the compressor belt or the alternator. One had likely failed and required immediate intervention by a Thermo King authorized dealer technician.
As soon as they received approval for intervention, an authorized dealer technician immediately got to work and managed to fix the problem before the train departed. They saved the entire shipment and avoided the additional CO2 associated with the production and transportation of meat.
Happy customer, happy Mark. “I feel great whenever we solve a case for our customer. I’m using what I learned from my experience and helping the customer even more than I could at the workshop,” he shares.
Delivering Premium Uptime and Exceptional Service
No matter the weather, no matter the time of day, Mark and the other experts at the Uptime Center are driven by their mission to deliver premium uptime, exemplifying the commitment to providing exceptional service and solutions; “We will continue our journey to deliver premium uptime to our customers, that’s what Thermo King is about.”
Curious about Thermo King’s 24/7 fleet monitoring? Check out the video below!
Related articles
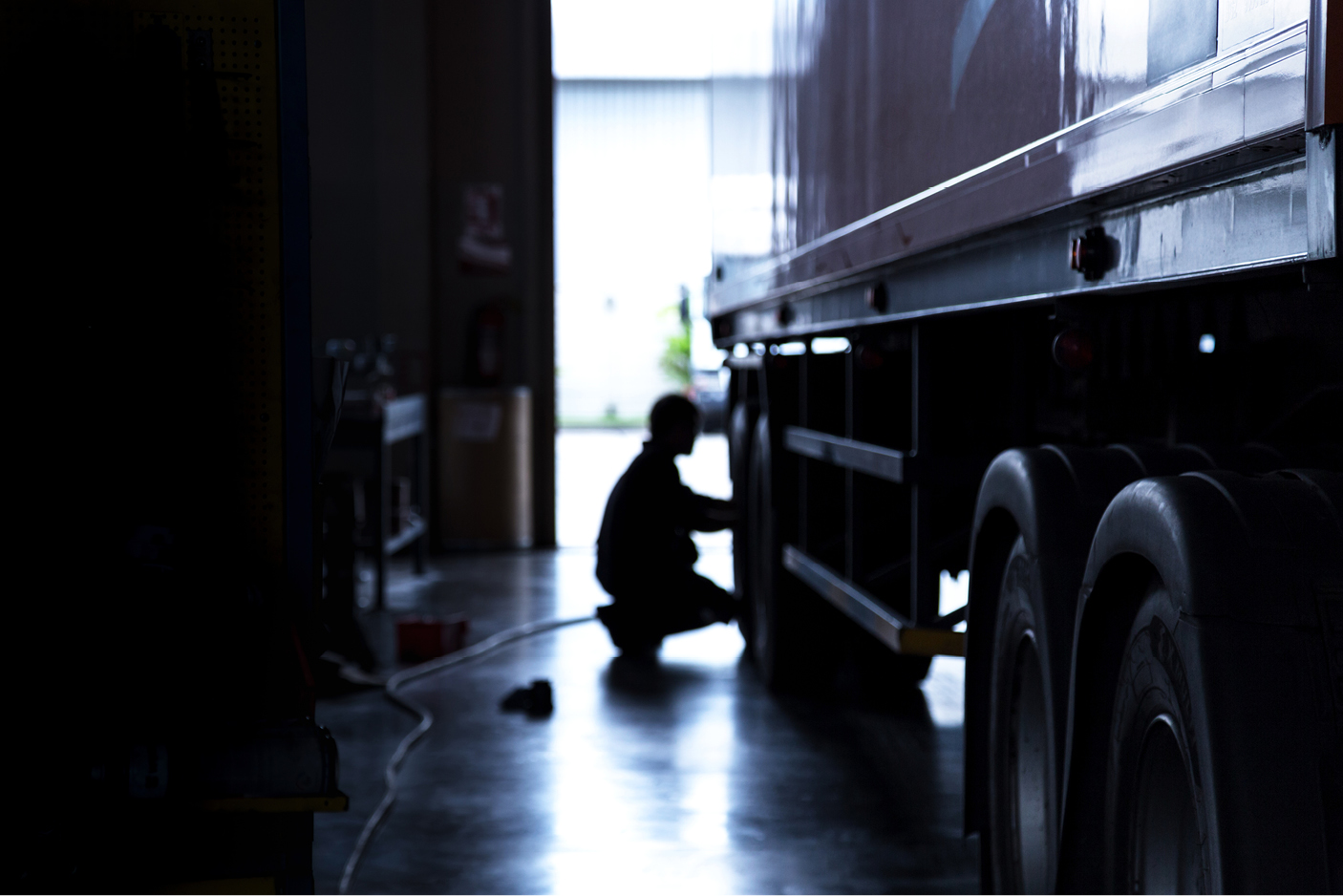
Extending your unit’s operational life span – our 5 top tips
Extending the life span of a refrigeration unit can provide a massive boost to your overall return on investment. Here we offer our 5 top tips for keeping your units running to their full potential for longer.
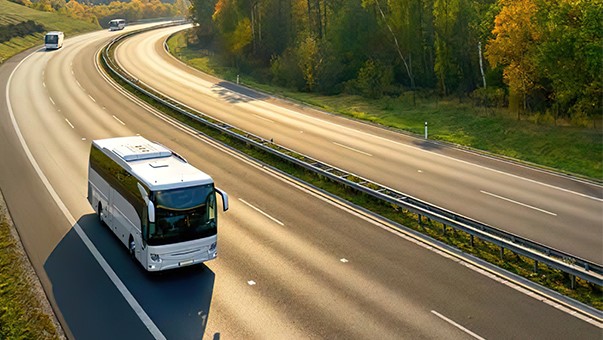
HVAC CO2 sensors for buses: Maintaining a healthy environment wherever you travel.
Increased fresh air supply and improved airflow on public transport helps to reduce the transmission of viruses. Stay in complete control of your environment with Thermo King’s new CANAIRE CO2 sensors.
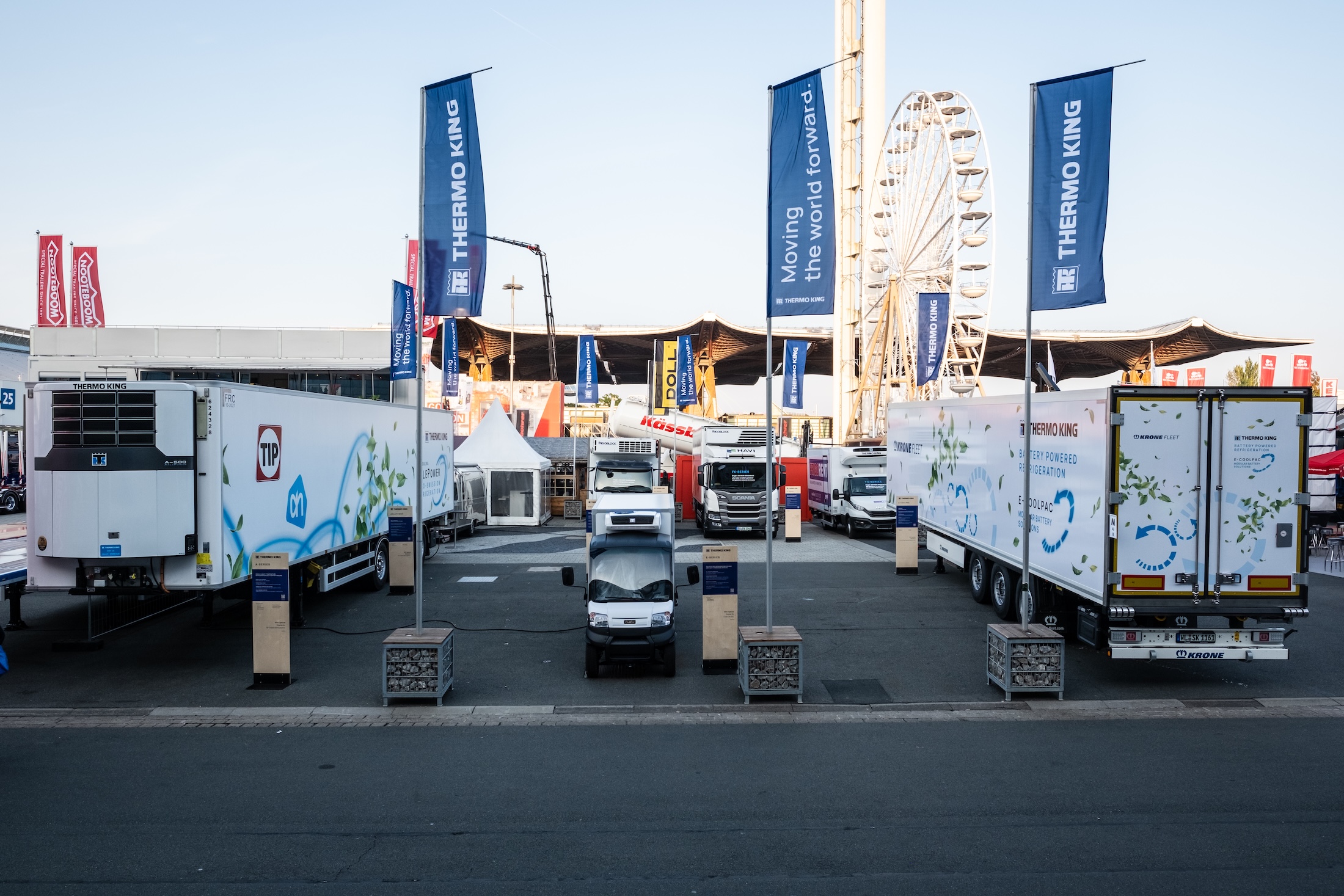
The top 3 cold chain trends driving industry progress at IAA 2024
IAA Transportation 2024 showed record attendance and powerful industry progress. Thermo King looks back, and forward, on 3 trends in refrigerated transport.